Brothers International can supply a full range of refractory products for all applications within this industry, including silica, fire clay, mid and high alumina shaped products as well as a complete range of basic bricks based on resin bonded technology.
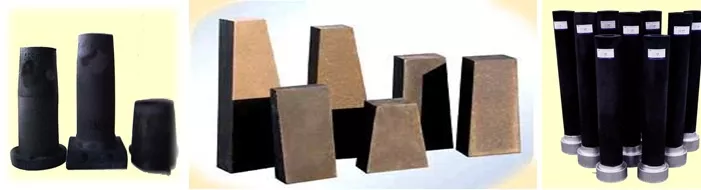
Refractory Product Range for the Steel Industry:
The BI portfolio also includes fired spinel, fired mag chrome, alumina graphites, tap holes and sliding gate flow control refractories.
Unshaped products such as castables, gunnings and rammings also constitute a large proportion of our sales to the iron and steel industry. Ancillary items, such as precast shapes, tuyeres and nozzles are also available.
Application for the Steel Industry:
1. Converter / Blast Oxygen Furnace: Brothers International can provide a full range of refractories products for BOF Converters.
The magnesia carbon refractories used in the working lining are based on a range of resin-bonded, high-purity fused and sintered magnesites and graphite. The choice of material is dependent on the operational parameters and lining design.
Some of the requirements are good hot strength, corrosion resistance, oxidation resistance and thermal shock resistance. Fused and resin bonded bricks are available for safety linings.
We can propose casting and gunning maintenance to materials for lining repair to improve and extend the campaign life of the converter lining.
2. EAF: BI supply all types of EAF refractories.
The optimal lining is selected according to your operational parameters.
We have developed a full range of magnesia carbon refractories, fired refractories and a variety of ramming and gunning material to suit your individual needs.
3. Ladle/refining ladle: BI supply a full range of refractories for ladle applications including ladle furnaces, VOD/VAC ladles, casting ladles and VD Processes.
For the working lining, we supply a range of resin bonded magnesia-based carbon-containing products.
Alumina Magnesia carbon is generally used in ladle sidewall, bottom and impact areas. A range of spinel and fired bauxite refractories can also be supplied for working lining.
For safety linings fireclay and mid to high alumina are supplied. BI supplies a full range of monolithics, cements, castables and ramming materials to complement theshaped products and maintain and repair linings.
4. Tundish: BI designs linings for use in tundish metal casting.
Materials are chosen for zones: roofs, wear, impact, dam, weir, baffell and permanent linings.
Bricks demonstrating refractoriness, resistance to thermal shock and volume stability line the furnace operation areas. Bricks include: magnesia carbon and alumina magnesia carbon.
Chemically bonded refractory castables exhibit strength and density combined with volume stability from ambient to elevated temperatures. Monolithics include: basic castables, slurry gunning mix and dry setting mix.
5. Reheating Mill Furnaces: Reheating furnaces heat steel billets, blooms and slabs from a continuous casting operation, to a rolling temperature between 900°C and 1500°C.
In steelmaking, this application is considered to be one of the most stable for refractories. We work to improve furnace lives and reduce downtime during installation and repair.
Reheating furnaces appear in a variety of designs including the two most widespread which are walking beam furnaces and pusher furnaces. Steel shapes and tonnage throughput play a key role in the choice of furnace design.
The choice of lining concept is dictated by a variety of conditions in different parts of the furnace. The lining properties include corrosion resistance, anti-spalling, abrasion resistance and thermal shock resistance.
Refractories used include magnesia bricks, high alumina bricks and fireclay bricks, as well as different types and qualities of monolithic materials