Brothers International Refractory products and engineering are well established in many applications :
- Refractory linings for the copper, nickel and lead industry
- Refractory linings for the aluminium industry
- Refractory linings for cement industry
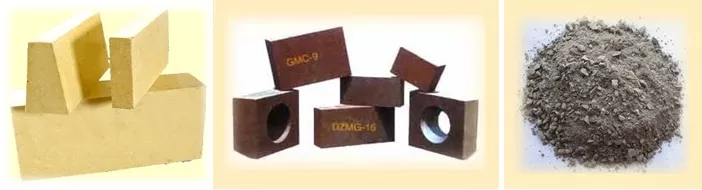
ALUMINIUM
Brothers International supplies lining materials for gas and electric melting furnaces both in the primary and secondary aluminium industries.
Product range:
Bricks: Carbon block; 70% & 80% high-alumina brick. Monolithics: carbon ramming masses; dry barrier mixes; plastic masses; 70 & 80% high-alumina castables gunning mass.
Precast and Equipment: Anchor articles; Silicate-calcium plates; Silicon-carbide plates.
Keeping up to date with trends in melting furnace linings, BI develops high resistant monolithic materials for cathode working areas as well as selecting materials to preserve heat in bath furnace areas. The choices of materials offer good thermal insulation characteristics and solid resistance to temperature changes.
COPPER, NICKEL & LEAD
Brothers International carries a full line of high-quality products for the primary and secondary production of non-ferrous metals. For copper, nickel and lead, we offer magnesite-chrome brick in many different formulations. From direct-bonded to fully re-bonded, and everything in between, Brothers International supplies brick made only from 100% virgin materials. Supplementing the brick line is a full catalog of specialties including mortars, castables, plastics and rams.
Product range:
Brothers International has all of the products required for your smelting needs. From magnesia-chrome working lining bricks to insulators, to back-up linings, to anchors and specialties, we have your needs covered. All of Brothers International’s products are designed to provide optimum service in your specific operation with your existing practice. By varying raw materials, firing schedules and post-firing treatments like salt impregnation, we can engineer a solution for you.
CEMENT
Brothers International designs linings for use in cement production. Materials are chosen for rotary kilns and kiln cyclone suspension precalciner. The rotary kiln divides into zones for: long, dry and wet processes (chain section feed cone, preheating, calcining); burning (upper transition, sintering, lower transition); and discharge. Installed “in front” of the cement rotary kiln to reduce the losses and enhance efficiency the suspension pre-heaters and pre-calciners have three zones including the hot face and safety linings as well as meal chutes.
Product range:
Mostly, bricks demonstrating refractoriness, resistance to thermal shock and volume stability line severe furnace operation areas. Bricks include: magnesia-spinel; magnesia-chrome (silicate bonded, direct bonded and rebonded); mid and high alumina (alumina content 50, 60, 70, and 80%); fireclay bricks (super, high, medium and low duties plus semi silica).
Castables coat areas exposed to less arduous service conditions, areas hard to reach and areas requiring repair. Chemically bonded refractory castables exhibit strength and density combined with volume stability from ambient to elevated temperatures.
Associated features include abrasion resistance. Monolithics include: fireclay; mid alumina (50 & 60%); high alumina (70 & 80%); and phosphate.